Enhanced Automated Visual Inspection Systems For Lyophilized Vials
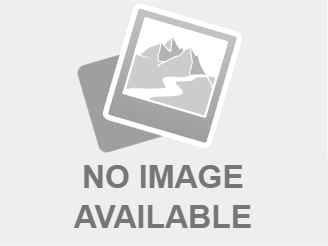
Table of Contents
The Challenges of Inspecting Lyophilized Vials
Inspecting lyophilized vials for defects presents unique challenges. Traditional methods often fall short, leading to inefficiencies and risks.
Limitations of Manual Inspection
Manual visual inspection of lyophilized vials relies heavily on human observation, leading to several limitations:
- High labor costs: Manual inspection is labor-intensive, requiring a significant workforce and incurring substantial labor costs. This cost increases exponentially with higher production volumes.
- Subjectivity and inconsistency in results: Human inspectors may have varying levels of experience and attention to detail, leading to inconsistencies in defect detection. This subjectivity introduces variability into the quality control process.
- Increased risk of human error leading to product recalls: Human fatigue and error can lead to missed defects, potentially resulting in the release of substandard products and costly product recalls. The consequences of such errors can be severe, impacting both the company's reputation and patient safety.
- Inability to inspect at high speeds required for modern manufacturing: Manual inspection cannot keep up with the speed and volume of modern lyophilization production lines. This bottleneck hinders overall production efficiency.
The Need for Automated Solutions
The limitations of manual inspection highlight the urgent need for automated solutions. Automated visual inspection (AVI) systems offer significant advantages:
- Improved accuracy and consistency in defect detection: AVI systems provide consistent and objective defect detection, identifying cracks, particulate matter, delamination, and other critical flaws with greater accuracy than manual methods. This ensures higher quality control.
- Increased throughput and reduced inspection time: Automated systems can inspect vials at significantly higher speeds than manual inspection, dramatically increasing throughput and reducing inspection time. This leads to faster production cycles and reduced lead times.
- Enhanced data management and traceability for improved compliance: AVI systems capture and store detailed inspection data, including images and defect classifications. This enhanced data management improves traceability and facilitates compliance with regulatory requirements, such as 21 CFR Part 11.
- Reduced operational costs in the long run: While the initial investment in an AVI system may be significant, the long-term operational cost savings—through reduced labor costs, fewer product recalls, and improved efficiency—make it a worthwhile investment.
Key Features of Advanced Automated Visual Inspection Systems for Lyophilized Vials
Advanced AVI systems incorporate several key features to ensure accurate and efficient inspection of lyophilized vials.
High-Resolution Imaging Technology
These systems utilize advanced imaging technology to capture even subtle defects:
- Advanced cameras with superior image resolution and sensitivity: High-resolution cameras ensure the capture of fine details, enabling the detection of even microscopic defects. The sensitivity of the cameras is crucial for identifying subtle variations in vial appearance.
- Different lighting techniques (e.g., dark field, bright field): Employing various lighting techniques optimizes the visibility of different types of defects. Dark field illumination, for instance, enhances the visibility of particulate matter.
- Integration with image processing algorithms for enhanced contrast and clarity: Sophisticated image processing algorithms improve contrast and clarity, enhancing the visibility of defects and facilitating accurate classification.
Sophisticated Algorithms and AI
Artificial intelligence (AI) and machine learning (ML) are integral to modern AVI systems:
- Machine learning algorithms for automated defect classification and identification: ML algorithms learn to identify and classify different types of defects based on training data, enabling automated defect detection and classification.
- AI-powered systems that learn and adapt to variations in vial appearance and defect types: AI systems continuously learn and adapt, improving their accuracy over time by adjusting to variations in vial appearance and new defect types. This adaptive learning ensures consistent performance even with changing production conditions.
- Reduced false positives and improved accuracy through continuous learning and optimization: The continuous learning capabilities of AI systems reduce the number of false positives, ensuring higher accuracy and minimizing unnecessary intervention.
Data Management and Reporting
Effective data management is crucial for regulatory compliance and process optimization:
- Real-time data acquisition and analysis for immediate feedback on production quality: Real-time data analysis provides immediate feedback on the quality of the production process, allowing for prompt adjustments and corrective actions.
- Detailed reports and visualizations of inspection results, including defect types and locations: Comprehensive reports provide detailed information on the types and locations of defects, facilitating root cause analysis and process improvement.
- Integration with existing quality management systems for seamless data transfer and traceability: Seamless integration with existing quality management systems ensures data integrity and traceability, facilitating compliance with regulatory requirements (e.g., 21 CFR Part 11).
Benefits of Implementing Enhanced Automated Visual Inspection Systems
The benefits of adopting enhanced AVI systems are substantial and far-reaching:
- Significantly reduced product recalls and associated costs: By reducing human error and improving defect detection, AVI systems significantly reduce the risk of product recalls and the associated financial and reputational costs.
- Improved product quality and patient safety: Higher quality control leads to improved product quality and enhanced patient safety, a critical priority in the pharmaceutical industry.
- Increased manufacturing efficiency and throughput: Automated systems significantly increase throughput and reduce inspection times, leading to improved manufacturing efficiency.
- Enhanced regulatory compliance and audit readiness: Comprehensive data management and traceability capabilities ensure regulatory compliance and streamline audit processes.
- Better utilization of skilled labor, allowing personnel to focus on higher-value tasks: By automating routine inspection tasks, skilled personnel can focus on higher-value activities, such as process improvement and quality control strategy development.
Conclusion
Implementing enhanced automated visual inspection systems for lyophilized vials is no longer a luxury but a necessity for modern pharmaceutical manufacturing. These advanced systems offer significant improvements in accuracy, efficiency, and compliance, ultimately contributing to higher product quality and patient safety. By adopting these technologies, pharmaceutical companies can reduce costs, enhance productivity, and strengthen their commitment to delivering safe and effective medications. Invest in advanced automated visual inspection systems today and ensure the highest quality control for your lyophilized vials.
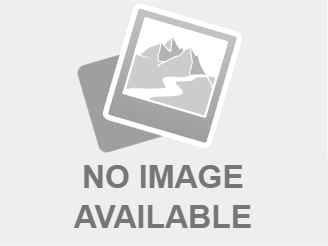
Featured Posts
-
Selena Gomez And Benny Blanco Accidental Glimpse Into Their Private Life
May 12, 2025 -
Jessica Simpsons Stylish Airport Look Cheetah Print And Blue Fur
May 12, 2025 -
Ufc 315 Early Predictions And Betting Odds
May 12, 2025 -
The Next Pope Nine Prominent Cardinals In The Running
May 12, 2025 -
Jamaica Observer Cooyah Unveils New Grand Slam Track Collection
May 12, 2025