Strategies For Effective Automated Visual Inspection Of Lyophilized Vials
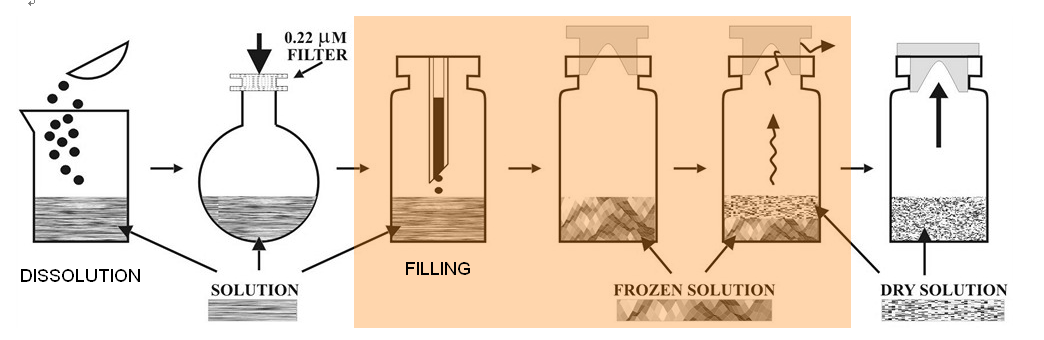
Table of Contents
Selecting the Right Automated Visual Inspection System
Choosing the right automated visual inspection system is crucial for successful implementation. The market offers a variety of technologies, each with its strengths and weaknesses. Key considerations include:
- Machine Vision Systems vs. Image Analysis Software: Machine vision systems typically integrate cameras, lighting, and software into a single unit, providing a comprehensive solution. Image analysis software can be integrated with existing imaging hardware, offering flexibility but requiring more technical expertise. The choice depends on existing infrastructure and budget.
- Key Features to Consider:
- High-Resolution Imaging: The system must have sufficient resolution and sensitivity to detect subtle defects such as cracks, particulate matter, or discoloration in the lyophilized cake.
- High Throughput: The speed of inspection must match or exceed production line speeds to avoid bottlenecks.
- Seamless Integration: The system should integrate smoothly with existing manufacturing lines and equipment (e.g., conveyor systems, labeling machines).
- Robust Data Management: Comprehensive data logging, reporting, and analysis capabilities are essential for traceability and regulatory compliance. This includes generating audit trails and detailed defect reports.
- Cameras and Lighting: Different cameras (e.g., CCD, CMOS) and lighting techniques (e.g., backlighting, ring lighting, coaxial lighting) are crucial for optimal image acquisition. The choice depends on the specific characteristics of the lyophilized vials and the types of defects being detected.
- System Validation and Regulatory Compliance: Rigorous validation is critical to ensure the accuracy and reliability of the system. Compliance with regulatory standards like 21 CFR Part 11 is essential for pharmaceutical applications. This includes software validation, hardware qualification, and operational qualification. A validated defect detection system is crucial for pharmaceutical automation.
Optimizing Image Acquisition for Lyophilized Vials
Lyophilized vials present unique challenges for automated visual inspection. The appearance of the lyophilized cake can vary, and cracks or other defects can be subtle. Optimizing image acquisition is crucial for accurate defect detection. Strategies include:
- Vial Presentation and Orientation: Consistent and accurate vial presentation is critical. Automated systems should ensure consistent orientation to minimize variations in lighting and image quality. The use of robotic arms or specialized conveyors can help achieve this.
- Lighting Techniques: Proper lighting is crucial to highlight defects and minimize shadows. Techniques such as backlighting, ring lighting, and coaxial lighting can be employed depending on the type of defects being inspected. Careful selection of light intensity and wavelength can further optimize image quality.
- Image Preprocessing: Image preprocessing techniques such as contrast enhancement, noise reduction, and image filtering can improve the quality of images and enhance defect detectability.
- Environmental Control: Maintaining consistent temperature and humidity is important to prevent changes in the lyophilized cake that might affect the image quality and inspection results. This contributes to consistent and reliable image optimization.
Developing Robust Defect Detection Algorithms
The heart of any automated visual inspection system lies in its defect detection algorithms. These algorithms analyze images to identify defects such as cracks, particles, and discoloration.
- Algorithm Types: Different algorithm types exist, including rule-based algorithms (defining specific rules for defect identification) and machine learning-based algorithms (training algorithms on large datasets to learn patterns and identify defects). Machine learning, including artificial intelligence, offers greater flexibility and adaptability.
- Algorithm Training: Robust algorithms require training with diverse datasets representing a wide range of vial appearances and defect types. This is essential to improve the accuracy and robustness of the defect detection system.
- False Positives and False Negatives: Minimizing both false positives (incorrectly identifying a non-defect as a defect) and false negatives (failing to identify a true defect) is essential. This requires careful algorithm design and training.
- Algorithm Updates and Retraining: Regular updates and retraining of algorithms are crucial to maintain accuracy and adapt to changes in the production process or the appearance of lyophilized vials.
Implementing Quality Control Measures and Data Analysis
Effective quality control is vital throughout the automated visual inspection process.
- Quality Control Measures: Implement rigorous quality control checks at each stage, from system calibration and image acquisition to algorithm performance and report generation. Regular performance verification is essential.
- Key Performance Indicators (KPIs): Track KPIs such as defect rates, inspection throughput, and false positive/negative rates to monitor system performance and identify areas for improvement.
- Data Analytics: Use data analytics to identify trends in defect rates, pinpoint process variations, and improve overall process efficiency. This data-driven approach to quality control allows for proactive adjustments.
- Regulatory Compliance and Reporting: Generate comprehensive reports for regulatory compliance, including detailed information on inspection results, defect types, and system performance. This ensures traceability and facilitates audits.
- Statistical Process Control (SPC): Utilize SPC methods to monitor and control the process, ensuring consistent quality and minimizing variations.
Mastering Automated Visual Inspection of Lyophilized Vials
Effective automated visual inspection of lyophilized vials requires a multifaceted approach, encompassing careful system selection, optimized image acquisition, robust defect detection algorithms, and rigorous quality control measures. By implementing the strategies discussed above, pharmaceutical manufacturers can significantly improve the accuracy, efficiency, and regulatory compliance of their quality control processes. Automation improves accuracy, increases throughput, reduces labor costs, and ensures enhanced regulatory compliance. Implement these strategies for effective automated visual inspection of your lyophilized vials today!
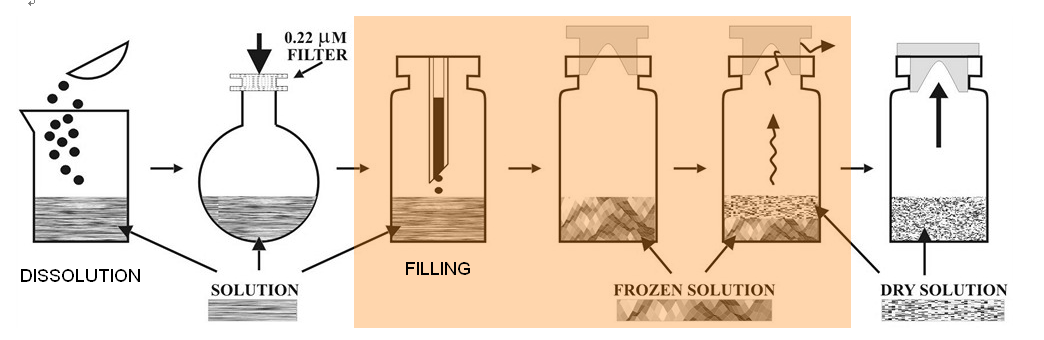
Featured Posts
-
Flight Attendant To Pilot Overcoming Gender Barriers In Aviation
May 11, 2025 -
Ray Epps Sues Fox News For Defamation Examining The January 6th Claims
May 11, 2025 -
500 Influential People In Washington Dc 2025 Edition
May 11, 2025 -
Thomas Muellers Bayern Munich Exit Reactions And Implications
May 11, 2025 -
Understanding The Jurickson Profar 80 Game Ban Email Implications
May 11, 2025